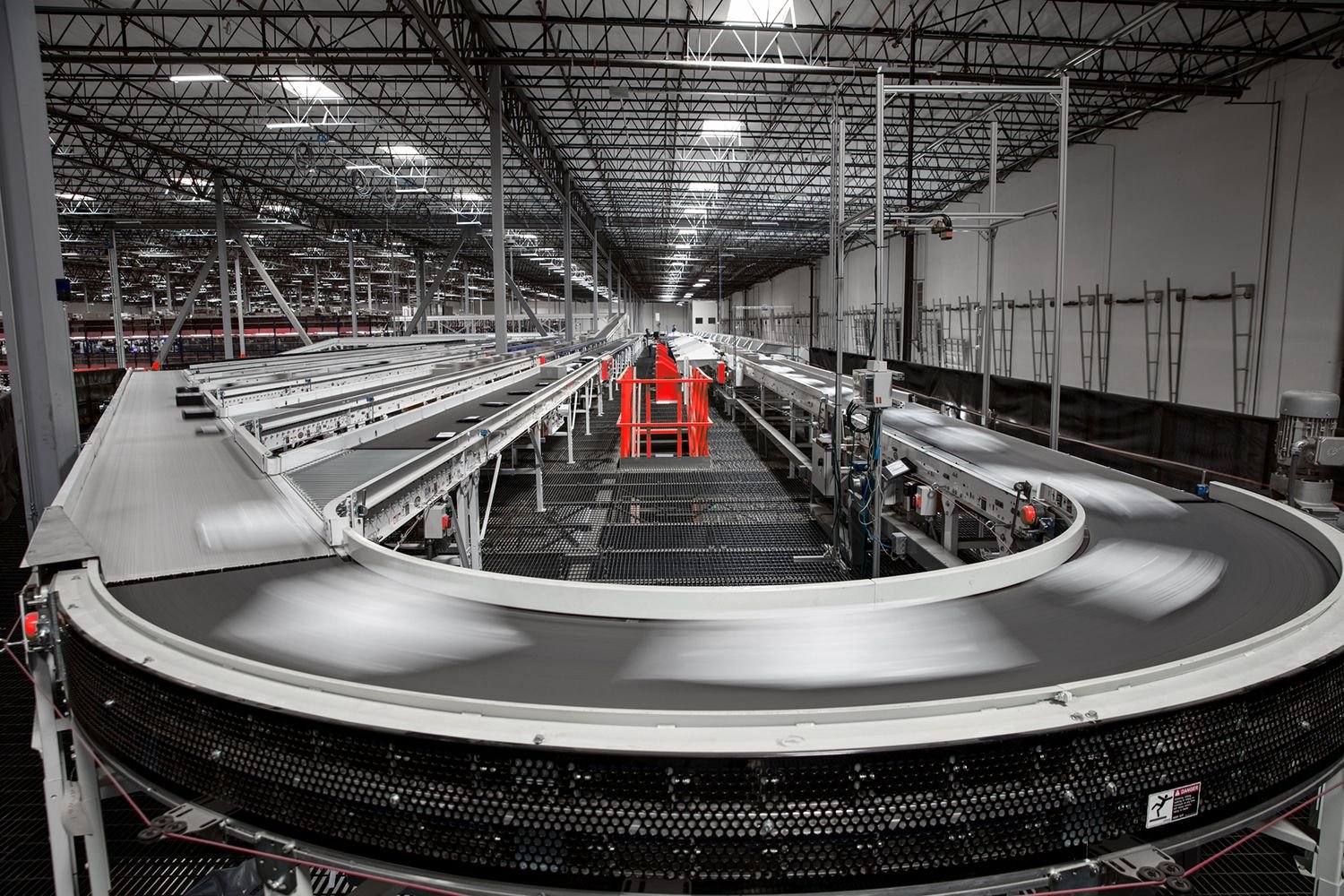
Frequently Asked Questions
Automation provides the ideal opportunity to significantly enhance warehouse and logistics operations, to become more streamlined, efficient, and cost effective. Whilst we have been transforming industries with bespoke automation solutions for nearly 30 years, we appreciate that many warehouse and logistics operators may be new to automation and have questions around the applications, benefits, investment opportunities and how to prepare their team for implementation. Recognising this, we’ve put together some frequently asked questions to cover many of the main queries around these topics. For more specific information, please get in touch with one of our expert team, we’d be happy to discuss your individual requirements and answer any questions you may have.
LAC FAQs
Introducing automation offers numerous benefits for today’s logistics and warehousing operators. Automation is highly versatile and can handle repetitive and time-consuming tasks faster and more accurately than human workers, leading to higher operational efficiency and productivity. By reducing the need for manual input for certain processes, businesses can minimise the risk of errors and reduce their overall cost for labour, as well as redeploying workers to focus on more value-added and strategic activities across the warehouse. Automated systems can operate 24/7 without breaks, allowing for continuous and increased speed of operation, from goods-in to final shipment.
Automated solutions are flexible and scalable, designed to handle varying workloads making it easier for businesses to respond quickly to changes and plan for expansion. Data tracking and analysis from automated systems also provide valuable insights that can inform business decisions and strategies that support long term growth.
Using automation to enhance productivity and accuracy of operations improves customer satisfaction and can provide a competitive edge by allowing a business to operate more efficiently and effectively than its competitors.
Automation solutions are increasingly more energy efficient thanks to advancements in technology and can operate with decreased lighting and heating than if using a manual workforce. Using automation enables operations to become more streamlined and effective in carrying out the required tasks, resulting in more efficient processes which typically consume fewer resources and generate less waste. Furthermore, improving supply chain efficiency and transparency through the integration of automation solutions, can help businesses to adopt more sustainable practices and reduce the overall environmental impact of logistics and transportation.
Using energy-efficient technology, for example robots and materials handling equipment, can contribute to environmental sustainability. Automation solutions such as our 24v conveyor modules are specifically designed to use low energy components and are manufactured here in the UK, lowering the carbon footprint and further enhancing the system’s environmental credentials.
In November 2023, the Government announced the availability of £4.5bn in funding for the UK Manufacturing industry, with British manufacturers able to take advantage of the package of loans and grants from 2025. The injection of investment for the future will enable manufacturers to look long term at increasing both productivity and sustainability through advanced technologies such as Automation. Furthermore, the government also announced the expansion of the Made Smarter Adoption programme, set to drive growth specifically for SME manufacturers. Already available in the North East, North West, West Midlands and Yorkshire & the Humber, the scheme will be offered across all regions in England in 2025/26 with plans to make it UK-wide in 2026/27. The goal of the scheme is to help small and medium sized manufacturing companies to use digital technologies which will enhance productivity whilst reducing the carbon footprint. With the significant cost and operational efficiencies to be gained through the adoption of automation technologies, seeking out financial support in the form of grants offers valuable support for businesses to explore automation solutions that have the potential to transform operations.
All automation systems require some form of maintenance to ensure they continue to operate efficiently and reliably. Most maintenance of our robust automation solutions is carried out via preventive and planned servicing. L-A-C has a dedicated Aftercare team who work tirelessly to support our customers and ensure our solutions continue to deliver excellence. We have a dedicated 24/7 breakdown call support which means that assistance is available immediately to help determine and rectify the problem. Additionally, we offer a comprehensive and flexible range of routine preventative maintenance contracts to ensure our systems and solutions continue to run as reliably as possible.
Our Remote Customer Software Support offers a swift response to your system needs, saving hours of potential downtime. Our intelligent software enables us to provide secure, non-intrusive connectivity between computers and your production line allowing live-feed data connection to be displayed and assessed remotely.
At L-A-C we design, manufacture and build our own systems at our facilities in Nottingham. This allows us to support our installations with the necessary replacement parts quickly and easily so you can avoid potentially long lead times or having to hold inventory taking up valuable space at your warehouse.
Fortunately not! Modern automation systems are no longer deemed accessible only for large scale operations and are increasingly affordable to SMEs. Automation technology can range from small lines of conveyors or a single robot palletiser, up to complex systems that seamlessly integrate numerous robotic and materials handling technologies that manage every operational process from goods-in and order fulfilment, to packaging and final despatch. This flexibility allows solutions to be implemented on a smaller scale and expanded over time during a live operation, meaning capex is spread over time. Automation offers exceptional efficiency and performance, streamlining operations with many operational and labour cost savings alongside productivity benefits and favourable ROI. Financial support in the form of Government grants can also be explored to assist businesses in the upfront investment in automation solutions.
Automation solutions can utilise many different technologies, each with their own level of standardisation and complexity. L-A-C design bespoke solutions that will often combine a number of automation elements e.g. conveyor modules, robotics, ASRS etc. so the final ROI may be determined by the level of efficiency and overall operational benefits, compared to the existing or previous form of inventory handling. Typically, this ranges for most installations between 1.5 – 3 years, but can be shorter if the automation solution has a more dramatic impact on existing operations. In all cases, L-A-C aims to design and install the most effective and efficient solution for your needs, so your ROI will be optimised.
Implementing an automation solution may seem like a daunting task but with preparation and planning it can become a well-orchestrated process. We fully understand and appreciate there may be several stakeholders involved who have questions or concerns around the installation, how it integrates with existing processes and how ongoing operations may possibly be affected.
As part of our design, installation and aftercare support service, L-A-C ensures that all stakeholders are fully onboard with the project from the outset. This can include pre-project workshops, regular project meetings and briefings, training sessions for managers, operators and maintenance personnel as well as ongoing support and optimisation. L-A-C combines knowledge with partnership that is in place for the long term; your success is our success.
Automation solutions are extremely flexible and there is no limit to how large or small operations need to be to benefit from a system. We work with companies of all sizes to provide a wide range of automation solutions. From a conveyor module used to transfer packed e-commerce items to the despatch area, to a robotic picking arm used to carry out repetitive tasks that are unsuitable for manual handling, automation can be implemented on a small scale, with big results.
As an example, we recently installed a conveyor and robotic system under the arches of London Bridge for Entocycle the UK’s leading insect technology company, to create a ‘Centre for Insect Technology’ where they could demonstrate their unique breeding and production eco-system to potential investor and customers through our fully automated solution. At the other end of the scale, we work with customers at large-scale facilities, recently installing a high-density goods-to-person order fulfilment and replenishment system (Exotec) for 3PL iForce at their 880,000 sqft multi-user facility in Northamptonshire.
Installing automation solutions has a positive effect for a business, enhancing productivity, improving accuracy, increasing overall operational efficiency and reducing labour costs. Implementing technologies such as conveyors and robots to perform repetitive and time-consuming tasks reduces the need for manual labour, and increases the speed, accuracy and consistency of activities whilst minimising the risk of errors and potential waste. Automation is also extremely agile and can be scaled easily to handle increased volumes without additional labour and its associated costs.
Investing in automation technology offers staff the opportunity to be redeployed to other areas of the business to focus on more complex, value-added activities, avoiding both physically demanding and monotonous activities. Additionally, new technologies provide an opening for workers to upskill and take on more supervisory or technical roles within the business.
Automation offers numerous advantages such as enhancing efficiency, productivity, and accuracy. One of the key benefits is increased efficiency, as automated systems can operate continuously without breaks, leading to higher output and faster processes. This also reduces the potential for human errors, improving accuracy and consistency. Automation can lead to cost savings in the long term by reducing labour costs and reducing waste due to errors or inefficiency. It also provides scalability to companies enabling them to remain agile and capable of adapting operations quickly and efficiently without the reliance on additional labour. In environments that are hazardous or carry out repetitive tasks, automation improves safety by removing workers from potentially dangerous activities. It also allows employees to focus on more strategic and creative work which enhances well-being and job satisfaction. Finally, automation provides real-time data collection and monitoring which enables better decision-making and faster responses to problems or changes in the market.
Automation offers a robust solution to today's operational challenges and is evolving rapidly to adapt to technological advancements. Automation increases efficiency and reduces human error, and increasingly uses emerging technologies like AI and machine learning. This enables the system to become more intelligent and adaptive in dynamic industries providing real-time data that supports strategic decision making. As a key factor in futureproofing automation is its ability to integrate with new technologies and adapt to shifting market demands, automation solutions should be designed with agility in mind. Modular solutions in particular can be adapted quickly and easily to incorporate new and different forms of automation technologies and processes to handle changing requirements as the business evolves and grows.
When choosing a conveyor and automation system, there are several key factors to be considered to ensure that the chosen solution meets operational needs efficiently. 1. The conveyor must be suitable for the type, size, and weight of the materials it will handle, to ensure it can support the load without damage or loss of throughput. 2. Consider the required speed of operations and the volume of items that need to be moved, to ensure that the system is sufficiently agile to handle peak volume rates. 3. Assess the available floor space and layout of the facility as this will influence the type of conveyor system to be used, for example, flexible systems using modular conveyors are ideally suited to smaller or dynamic spaces. 4. Assess the level of automation needed; this could range from a fully automated system for repetitive tasks, or semi-automation required to work alongside human operatives. 5. Consider the durability of the system and its maintenance requirements, especially for heavy-duty or continuous operations. 6. Consider the initial investment and long-term operational costs as well as the cost savings gained from a reduction in manual labour, waste and increased productivity.
All industry sectors can benefit from automation in one form or another. Our core industry sectors where we provide innovative automation solutions including automotive, healthcare, grocery, retail, e-commerce, 3PL, food & beverage, and manufacturing. Solutions range from modular conveyors to fully integrated conveyor systems, Automated Storage and Retrieval Systems, robotics such as Autonomous Mobile Robots for goods-to-person operations, as well as palletisers and shuttle systems. Automation offers a wide range of benefits across efficiency, productivity and accuracy, with additional cost savings due to a reduction in manual labour.
An automated system can be designed to weigh and separate products in an efficient way to streamline operations. This type of system often incorporates integrated weighing sensors and sorting equipment, for example, diverters, pneumatic arms, or conveyor belts with adjustable routes for certain products. For weighing tasks, the system may use precision sensors to measure the weight of each product as it moves along the conveyor. This data can then be used to ensure products meet weight specifications for quality control or specific categorisation. Separation processes are usually based on weight, size, or other predefined criteria, where the system can automatically separate products into different categories or channels. For example, heavier items might be diverted to one conveyor line, while lighter goods go to another conveyor line. This level of automation is commonly used in industries like food processing, packaging, and manufacturing, improving efficiency by reducing manual sorting and ensuring accuracy in product handling and classification. Additional automated processes can be integrated to include sealing bags, placement in boxes and labelling, as well as robotic palletising to offer a fully automated solution for all stages of production and materials handling.
To design and deliver an operational ASRS solution typically takes between 6 and 12 months. This is in part due to the supply chain lead times, testing and physical installation phase on site which can vary depending on size and complexity of requirements. Additionally, part of the design process incorporates in-depth data analysis of current and planned operations, to determine vital information such as volumetric and throughput data. Once the requirements have been established, this data becomes the intelligence behind the L-A-C design for an ASRS system to ensure we provide the optimal solution for each customer requirement.
As each L-A-C design is bespoke, we encourage you to take advantage of our FREE automation audit, where we can assess your needs and provide you with an outline of potential solutions, alongside more accurate lead times.
A new conveyor and automation system can significantly enhance productivity and efficiency. Automated conveyors streamline the movement of materials, which reduces the time needed to transport products between process stages, leading to faster workflows and increased productivity. By automating repetitive tasks, such as sorting, packaging, and transporting goods, a conveyor system reduces the need for manual labour, allowing workers to focus on more value-added tasks. Automation minimises the potential for human error, ensuring consistency across handling, sorting, order picking, and packaging tasks, which improves product quality and reduces rework or waste. Conveyor systems can run continuously without breaks, leading to higher throughput to meet production targets more easily, and are designed with agility in mind, to offer the required capacity to handle peaks in order volumes or throughput. Automation also reduces the need for human intervention in potentially hazardous tasks, such as heavy lifting, minimising workplace accidents and downtime. Collectively, all these factors enhance the overall operational efficiency and productivity of manufacturing, production and logistics materials handling tasks.
For nearly 30 years L-A-C has designed and manufactured its own portfolio of conveyors, automation and robotics technologies, bringing the latest innovations to customers in a wide range of industries. We have a dedicated 70,000 sqft facility in Nottingham where we manufacture and assemble our conveyor and robotics ranges. Manufacturing here in the UK offers many benefits to customers, not least in shorter lead times and a controlled supply chain. Additionally, our expertise allows us to continually revise and re-engineer our range of automation technologies to take advantage of new innovations as they become available.
L-A-C is proud to have a global presence with numerous installations across Europe, China, Australia and America. Our recent acquisition by MotionTech enables us to become an integral part of their growing portfolio of industry-leading engineering and automation companies, following our core values of providing engineering excellence and innovation to our customers through our robust, high-performance solutions, that are both fit-for-purpose and future-proofed. The partnership allows us to further expand our dominance into Europe and worldwide, delivering efficient warehouse automation and robotics solutions to customers in a wide range of industry sectors.
L-A-C takes a pro-active and collaborative approach to working with our customers. As part of the consultation phase we establish what your existing operations look like and we regularly visit our customers' operations as part of this process, to fully understand all areas of the business, current and future. We can then use this information and operational data to design the most appropriate automation solution to enhance efficiency and productivity of your operations.
Quick Links
CONTACT US
Unit 3, Charles Park Cinderhill Road, Bulwell, Nottingham NG6 8RE
0115 975 3300
Sales enquiries: sales@lacgroup.co.uk